As product designers, ideally we aim to create products that serve humanity. However, an often overlooked nuance is that when people and organizations buy products, they’re buying ownership, not just usage. Ownership provides experience and carries responsibility over time. This perspective is crucial even for single-use products, where there are costs and tradeoffs to keeping one’s investment short-term. In recent decades, usability and user experience have become more evident in product design, but many developers miss the larger portion of the iceberg: the cost and performance drivers that lie beneath the surface.
Ownership costs, for both developers and customers, are profoundly influenced by the human element. It’s not just about the end-users. Significant costs stem from every human involved in the product’s lifecycle – manufacturing, testing, training, operation, and maintenance. And as designers, we need to remember that each one of these humans counts. That’s where Human Systems Integration (HSI) comes in. HSI is the systems engineering process by which all of the humans that count are considered. HSI allows us to create products that not only serve effectively, but that are economically sustainable for both the provider and the consumer.
Hardware + Software + Human
Historically, product designers have focused on the technical capabilities of a system more than on the human interactions with and within systems. HSI shifts the paradigm of systems thinking and requires that we redefine the ‘system’ as consisting of Hardware + Software + Human. This reframing enables us to maximize total system performance and minimize life-cycle costs.
With human factors, user experience and usability become paramount in product design. It’s essential to also integrate considerations for manufacturing, training, operation, and maintenance into the earliest phases of the product design cycle. This approach is critical. By the time a product has completed the preliminary design phase (less than 25% of the way through the effort), design decisions have already committed 85% of the product costs. And the cost to extract defects and design issues is already 20-100x greater than it was in the concept phase.
The Space Shuttle
One large-scale system that highlights the need for HSI is the Space Shuttle. When it was conceived of in the 1970s, it was promised to be a cost-effective way to access Low Earth orbit, with a projected launch rate of 40 flights per year. This would necessitate a ground processing time of 5 weeks and 3 fleet vehicles. In reality, over its 30-year life, the Shuttle averaged only 4.5 launches per year. One main reason for this was the focus on vehicle performance requirements over consideration of human-centered operations and maintenance requirements during the design phase. Minimizing the number of personnel, component accessibility, procedures, and tools required to turn it around was not considered, nor baked into the design. As a result, it failed to meet its projected launch rates.
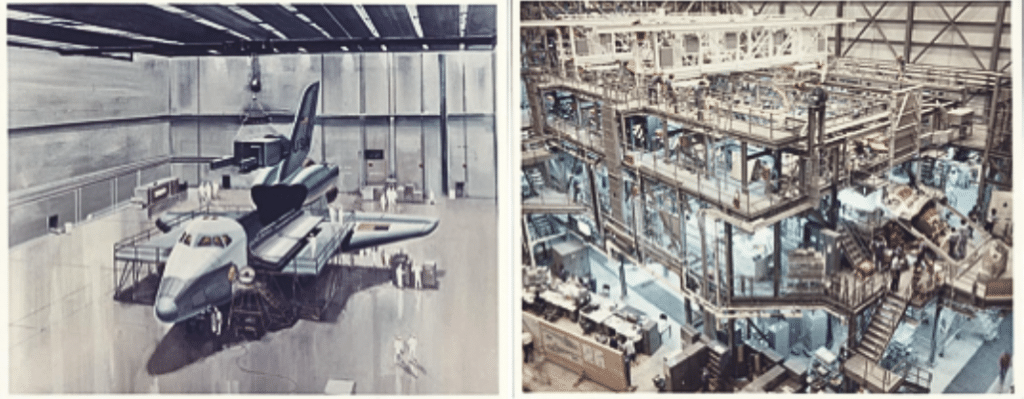
To gain control of escalating costs and enhance performance, the U.S. Department of Defense formally mandated HSI in the early 2000s. But despite this early adoption within the military, many product designers are still not fully aware of the scope of HSI. Its multidisciplinary approach is not emphasized in industry. And for some products with smaller scope or less complexity, the full implementation of HSI may seem impractical or excessive. Yet, recently, data has shown that about 80% of software life-cycle costs occur during the maintenance phase. That is due to unmet or unforseen requirements and usability issues. Success stories such as American Airlines and IBM demonstrate substantial cost savings and efficiency improvements when HSI principles are applied early in the design phase. Various industries’ cost- benefit ratios have been reported as high as 1:100.1
Products serving humans that count
Integrating HSI is a technical necessity to building products that count. It’s also a commitment to sustainable ownership and usability. It’s not just about adopting a process but embracing a mindset that values every human in the product’s lifecycle as part of the system. In this way, we innovate sustainably for the future and create products that truly serve.
- “Cost Arguments and Evidence for Human Factors Integration.” Systems Engineering & Assessment Ltd. Defense Technology Centers. HFI DTC Issue 1, October 2006. ↩︎